About Expert
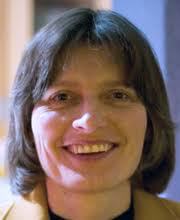
Key Topics
1. Prepare a report which consists of:
a. a sample of maintenance-related problems at your work Place.
b. discussion on how TPM and OEE concept can lmprove maintenance work
2,Conduct OEE analysis on a machine at your workplace and findings. Suggest at least 5 ways on how to situation.
The maintenance related problems occurring in the workplace
The maintenance work can be hazardous in its way. The maintenance workers are exposed to various hazards in the workplace as they have the responsibility of carrying out a long range of activities at the workplace. These hazards can be divided into various types namely physical, biological and others.
The physical hazards in management include the following problems:
Exposure to noise: It is usually due to working on or using a noisy equipment/ machine.
Vibrations: These physical hazards are especially experienced during the maintenance of tunnels, roads, or bridges).
Working at height has the risk of falls or falling of heavy tools and equipment.
Gaining access to hazardous equipment usually confined environment that can lead to injuries in various parts of the body.
Electrical hazards leading to burns and short circuits with high shock.
Excessive work conditions like high heat or high cold.
Excessive workload leading to critical physical condition and strenuous movements that include the carrying of heavy materials, pushing and pulling, kneeling, etc.
Exposure to harmful chemicals that are usually used for the maintenance of the machines.
Legionella exposure due to water systems and installation of air conditioners in the workplace etc.
The maintenance workers are further at a high risk of almost all types of accidents. Most of the accidents occur due to contact with dust or smoke particles, vapor or harmful gasses. The fibers like glass fiber and asbestos etc. also cause risks of accidents. The workers working in the workplace during maintenance tasks come in contact with toxic chemical substances causing further problems.
While the physical hazards have been mentioned, maintenance of instruments, water supplies etc. come under biological hazards. Due to the varying characteristics of maintenance work, the workplace is also prone to psychosocial hazards. The productivity of the workplace usually gets lowered during the maintenance work and causes urgency for restarting the activities soon. This practice puts the workers under significant pressure for completing the work as soon as possible. Further factors leading to more stress in the workplace include limited time, high pressure and low quality of work in the organization.
Other problems during the maintenance work in the workplace is the communication problem between the workers and contractors.
Some of the major issues or problems are discussed further in detail:
Access - Access in and around building where maintenance is going place along with the access to the equipment require during the maintenance procedure can be problematic. Some of the activities undergoing maintenance must require the work to be done in confined places and direct access to these place can cause glitches. Further risks related to work in confined spaces include asphyxiation.
Chemical and dust exposure –It is common for the maintenance workers to be prone to the chemicals that are toxic in nature as they are regularly used during the maintenance process and in the equipment that is being used during the whole process. This issue is not only related to the office or factories but is significant in every industry where the workers are maintaining or repair any office equipment. Further, exposure to dust particle is also an issue which causes skin irritations and breathing problems in the workers.
Asbestos – This issue has been encountered in almost millions of workplace and still is un-marked. It is usually not known to the employers, or the workers are intentionally not briefed regarding the issue. The workers especially the carpenters, fitters or plumbers are at a high risk of being affected by the asbestos. (O. ALLI, 2009)
Equipment and machinery – When the equipment is not entirely disconnected or isolated, they pose a great threat to the well-being of the workers. This includes risks of electrocution or to the moving parts of the body.
Musculoskeletal problems – The maintenance work at the workplace include bending, kneeling, and pulling, pushing and repetitive work with great force. This causes cramped space and increases the risks of musculoskeletal problems.
Many studies have indicated that these occupational hazards and workplace-related health issues like hearing problems, cancer, musculoskeletal problems, silicosis, asbestosis, etc. are seen in a large quantity of the workers who are associated with the maintenance employees. These employees are expected to develop the occupational health problems in high probability as compared to the average population.
The concept of TPM and OEE and their effect on maintenance of work
Total Production Maintenance (TPM) is considered as the medical science of the equipment and machines. TPM can be described as a maintenance program involving a newly defined innovative for maintenance of the plants and the machinery. TPM aims to increase the production along with increasing the job satisfaction among the employee with high employee morale. TPM highlights the importance of maintenance in business by considering it as a necessary or vital part of the workplace. The down time in the maintenance is usually schedules under the manufacturing day and in some parts as an essential part of the whole process of manufacturing. The main goal is holding the emergency and the unscheduled maintenance at as minimal as possible.
TPM can be introduced in any workplace for achieving the many goals. Some of the most important goals that can be achieved:
Avoids the accumulation of the wastage in the rapidly changing economic surrounding of the workplace.
Avoids the reduction of quality of product while high production of goods.
Decreases the costs.
Helps to produce the low batch quantity at the shortest time possible.
The goods sent must be non-defective. (Miyake, 1995)
Production
Helps to obtain minimum 80% OPE (Overall Process Effectiveness)
Helps to obtain minimum 90% OEE (Overall Equipment Effectiveness)
The machines are made to run even during break time. (Break time is for operators but not for equipment and machines)
Quality
The operation is done in a manner that there are no complaints from customers.
Cost
The manufacturing cost is reduced by around 30%.
Delivery
Aids in achieving 100% success in delivering the requirements of the customer.
Safety
Helps to Maintains accident-free surrounding.
Multitasking
The suggestions are increased by three times. The multi-skilled, as well as flexible workers, are developed.
The table below focusses on the improvements that can be seen in the workplace.
Motives of TPM
Uniqueness of TPM
TPM is different from other methodologies as the operators are made to encompass the whole process of maintenance. The concepts that are not followed include: "I (Production operators) Operate, You (Maintenance department) fix.
TPM Objectives
Aids in achieving zero defects, zero accidents and zero breakdown in each and every functional areas of the organization.
Helps to involve all the employee at every level of the organization
Reduces the defects as well as the self-maintenance.
Direct benefits of TPM
Aids to increase the productivity and doubles the OPE (Overall Plant Efficiency)
Rectified the complaints of customers.
The manufacturing cost is reduced by 30%.
The customers' needs must be satisfied which helps to deliver right time quantity, of appropriate quality.
Reduces the chances of accidents.
Follows the measure of pollution control. (Miyake, 1995)
Indirect benefits of TPM
Increases the level of confidence among the employees.
Work places are kept clean, hygienic and attractive.
The attitude of the operators has favorable changes.
Focusses on team managements for achieving the goals.
Horizontal deployment of innovative ideas in all functional areas of the organization.
Helps to share the information and experience. (Miyake, 1995)
OEE (Overall Equipment Efficiency) =
OEE = A * PE * Q
Where,
A= availability of the equipment and machines as a function of scheduled uptime.
A= (Mean time in between the failure – Mean time for repairing) / Mean time in between the failure. Where, the mean time in between the failures = (Total running time)/ Total number of failures.
PE= Performance Efficiency. It can be calculated as a product of rate efficiency and the speed efficiency. Where,
The rate efficiency can be defined as the actual average cycle time that is slower than the design cycle time due to various reasons including jams. The jams result in reduced output. And the actual cyclic time that is slower than the design cycle time machine output is declined as the machine is running at a lower speed.
Q= the quality rate that can be defined as a percentage of the parted out goods out of the total production. It is referred to as yield in most of the cases.
Implementation of the appropriate OEE in the work place helps to bring about the financial profits from the manufacturing operations. (Loughlin, 2003)
The major benefits that the implementation of OEE brings about are mentioned as below:
Downtime cost is reduced: When one of the most important or vital machine/ equipment undergoes breakdown, the operations going on in the organizations come to a standstill resulting in effecting the delivery in a negative manner and therefore impacting the cash flow process and decreased revenues.
Repair Costs are reduced: The implementation of OEE helps to predict the maintenance requirements therefore reducing the repair costs. When the historical database regarding the downtime faults increases to grow, then the maintenance department of the organization can predict the reasons and the impending failure. The workplace can also interface the OEE systems to the Computerized Maintenance Management System or CMMS, and can take proactive measures for predicting the maintenance. For example, when deciding on the impending failures, the maintenance department can order the critical parts at cheaper rates. Further, the workplace can save their cost be allocating the repair personnel during the emergency hours beforehand.
Labor Efficiencies are increased: The manufacturing companies can downsize themselves, especially during severe economic conditions. Therefore, the manufacturers feel a need to optimize the productivity and output of their existing workplace. The implementation of OEE is beneficial in these cases as it identifies the reasons for operator downtime along with productivity data. This knowledge helps the management to judge the allocation of resources on the basis of the personnel productivity. Further, OEE is beneficial for identifying the additional capacity of the mangers within the existing workplace during the better business climate.
The quality costs are reduced: Implementation of OEE helps to identify the total number of produced parts, the defected items and the reasons for the defect. It helps to identify the quality of work being done in the workplace. By implementation of OEE, the production managers can easily identify the main causes and help to decline the expenses incurred during the rework or scrapping. This improves the focus of organization in quality work and reduces the warranty costs.
Personnel Productivity is increased: The OEE systems helps the work to go paperless. This decreases the clerical time spent on recording, reporting, analyzing of the reasons of downtime by the operators as well as the supervisors. The paper work increases the level of explanation being done in the management. The implementation of OEE helps to capture and report the downtime along with the causes and therefore increase the efficiency of the workplace. This helps to save time that was lost in reporting the activities and further helps the working personnel for focusing on most important tasks. Thus implementation of OEE helps the worker to be informed regarding the work being done. ("A Manager's Guide to Overall Equipment Effectiveness (OEE) : Modern Machine Shop", 2005)
Production Capability is increased: When the downtime of the machinery is reduced, the productivity of the operators is increased, and further, the defects are reduced. This helps to achieve better results during the production with the same resources and same workplaces.
Cost Estimation: The OEE system is scalable, and the cost of the system can easily be scaled for yielding better results. Taking example of a case where the manufacture can easily start the process by implementation of a pilot system. This system can encompass all the manufacturing cells and can think of the opportunities of the improvements in the organization. The implementation and size of the pilot system are the factors that influence the manufacturers cost. The following is the list of variables that affect the estimated cost the pilot system:
Total number, complexity and type of reports required
Total number of users who access the system
Total number of manual data entry terminals along with the mechanism for data entry which include the bar code reader interface and the biometrics interface.
Total number of machines required being interfaced
A total number of parameters for monitoring per machine. (Abdul Samat, Kamaruddin & Abdul Azid, 2011)
Conduction of OEE Analysis on a machine at workplace
The data for the machine undergoing the OEE Analysis are mentioned below:
Machine Data
Machine Data Values
Shift Run 480 min
Breaks 60 min
Run Time 375 min
Setup Time 15 min
Total Count 360
Downtime 30 min
Ideal Cycle Time 1 part every 63 seconds
Total Time 420 min
Target Counter 400
Good Count 355
Production Data
Production Data Calculated Values
Run Time 375 Total Production Minutes per Shift Run Time
Down Time 60 Total Downtime Minutes per Shift Down Time
Break Time 30 Total Break Minutes per Shift Run Time
Setup Time 15 Total Setup Minutes per Shift Setup Time
Good Count 360 Good Parts Produced per Shift Bad Count
Target Counter 400 Expected Parts per Shift Target Counter
Total Count 360 Total Parts Produced per Shift Total Count
Process Data
Data Formula Result
Total Time Setup Time+ Run Time+ Down Time 420
Run Time Total machine Production Time 375
Good Count Total number of good parts produced 355
Implementation of OEE and its variable
Variable of OEE Formula Result (in %)
Availability Run Time / Total Time 89.29
Quality Good Count / Total Count 98.71
Performance Total Count / Target Counter 90
OEE A*P*Q 79.56
The variable used in the OEE calculation that includes the following:
Availability: This factor takes into account all the kind of Down Time Losses.
Performance: This factor takes into account all kinds of Speed Losses.
Quality: This factor takes into account all the Quality Losses.
Now, considering the Target Counter interval time that is also called the Ideal Cycle time = 1 part every 63 seconds, therefore it can be said that the 400 parts are produced in the total time of 420 minutes of the equipment or the machine undergoing the OEE analysis.
Whereas on reducing the downtime by 900 seconds or 15 minutes, it can be concluded that the machine can produce exactly 14 extra parts. Calculations are shown as given below:
(15 minutes or 900 seconds * 1 part per 63 seconds) = 14 extra parts.
This improves the availability of the machine as the run time now becomes= 375+ 14 = 389.
Availability= 389/ 420= 92.72 %
This improves the performance as the total count increases to = 360+14= 374
Performance= 374/400= 93.50%
Further, the quality also improves due to change in good count as well as total count
Quality= 369/374= 98.64 %
Due to drastic change in all the OEE dependent variable, the simple OEE changes,
OEE= A*P*Q
OEE= 0.9262* 0.9350*0.9866 = 85.44%
It is therefore clear that with the decrease of 15 minutes or 900 seconds of the downtime, the OEE increases by almost 6 percent.
The downtime can be concluded to be a significant factor for improving the OEE as it is impossible to address the other related metrics while the process in not running. Thus the company needs to have constraints in the capacity along with deep consideration of factors like added overtime, buying a new equipment for increasing the productivity or hiring large number of employees. The idea is to invest the capital for optimizing the performance of the machines that are existing in the workplace as these can outweigh the expense incurred while buying the new machinery or equipment. Therefore, a way is to reduce the downtime, minimal setup time along with high improvement in the performance of the operator the company can easily unleash the capacity hidden in the workplace and can easily increase the benefits from implementation of the OEE. The table placed below is listing the World Class Goals for every metric value important the for calculation of OEE.
Metric Value World Class Value (in %)
Availability 90
Performance 95
Quality 99
OEE 85
Source: ("World-Class OEE – Set OEE Targets To Drive Improvement", n.d.)
The average OEE value calculated in our workplace was calculated out to be 79.86% while the World Class standards for OEE metrics for the factors are mentioned as given below:
Availability Performance Quality Simple OEE
World Class 90 95 99.9 85
In workplace 89.29 90 98.71 79.56
In case the OEE metric i.e. the variable of Availability, Quality, Performance, Simple OEE are higher than 100%, then the method of defining the metrics have not been used correctly. The possible case may be that the capacity is either underestimated during the process when the parameters while inputting the process. Usually, the performance variable is not calculated correctly.
The OEE data collection has to be automated and then again the plant information has to be collected by installing the related Production Marquees. With all the real-time machinery information, the management in the workplace as well as the machine operators, can therefore, react to the knowledge as well as the alarms that are displayed on the plant monitor. This way the simple OEE metrics can be collected from the manufacturing plant. ("International conference on sustainable manufacturing and operations management", 2013)
The use of OEE for improving the overall performance of the manufacturing system. Thus it is concluded that OEE acts like an improvement tool and the data can be used for enhancing the productivity at the workplace. The adoption of OEE in the workplace helps to reduce the downtime and further reduces the rework to the minimal level. Thus the correct outline calculation must be done for calculating the OEE at all the levels. In order to get benefits from the, OEE the workplace should ensure regular monitoring of the OEE value.
O. ALLI, D. (2009). National Profile on Occupational Safety and Health (1st ed.). Mauritius: Ministry of Finance. Retrieved from http://www.ilo.org/wcmsp5/groups/public/---ed_protect/---protrav/---safework/documents/policy/wcms_356031.pdf
Miyake, D. (1995). Improving manufacturing systems performance by complementary application of just-in-time, total quality control and total productive maintenance paradigms. Total Quality Management, 6(4), 345-364. http://dx.doi.org/10.1080/09544129550035305
Loughlin, S. (2003). A holistic approach to overall equipment effectiveness (OEE). Computing And Control Engineering, 14(6), 37-42. http://dx.doi.org/10.1049/cce:20030608
Abdul Samat, H., Kamaruddin, S., & Abdul Azid, I. (2011). INTEGRATION OF OVERALL EQUIPMENT EFFECTIVENESS (OEE) AND RELIABILITY METHOD FOR MEASURING MACHINE EFFECTIVENESS. The South African Journal Of Industrial Engineering, 23(1). http://dx.doi.org/10.7166/23-1-222
A Manager's Guide to Overall Equipment Effectiveness (OEE) : Modern Machine Shop. (2005). Mmsonline.com. Retrieved 30 March 2016, from http://www.mmsonline.com/articles/a-managers-guide-to-overall-equipment-effectiveness-oee
World-Class OEE – Set OEE Targets To Drive Improvement. Oee.com. Retrieved 30 March 2016, from http://www.oee.com/world-class-oee.html
International conference on sustainable manufacturing and operations management. (2013). In ISOM 2013 (p. 268). Mauritius.