Table of Contents
Total Quality Management (TQM) has emerged as a key concept for success in the intricate and constantly developing commercial world. TQM is a management strategy that relies on the involvement of all of the constituents of an organization including its workforce. It aims to achieve long-term success through customer satisfaction. This strategy benefits the organization as a whole as well as the general public. However, being a student, you might be wondering about what is total quality management, TQM principles, its importance, etc. Don’t worry! This detailed blog of All Assignment Help will give every important information that you need to know about TQM.
So, let’s get started!
What is Total Quality Management?
TQM was first introduced in the 1950s and began picking up popularity globally in the 1980s. Today, it is a cornerstone of many prosperous businesses all over the world.
Total Quality Management (TQM) is an organized way to manage an organization as a whole through constant improvements in response to input. Its goal is to raise the overall quality of goods and services.
Basically, total quality management (TQM) is about creating an environment where workers at all levels are committed to upholding high standards of performance in all facets of an organization’s operations. It’s a continual process that involves all organizational components cooperating to achieve shared objectives of quality and improvement rather than a one-time effort.
Students are asked to write assignments on different areas of TQM be it the total quality management process, benefits of total quality management, or any other. All students can’t write an efficient assignment. In such a case, they can get help with assignment online from subject-matter experts.
Read Here: Change Management: Why It Is Important
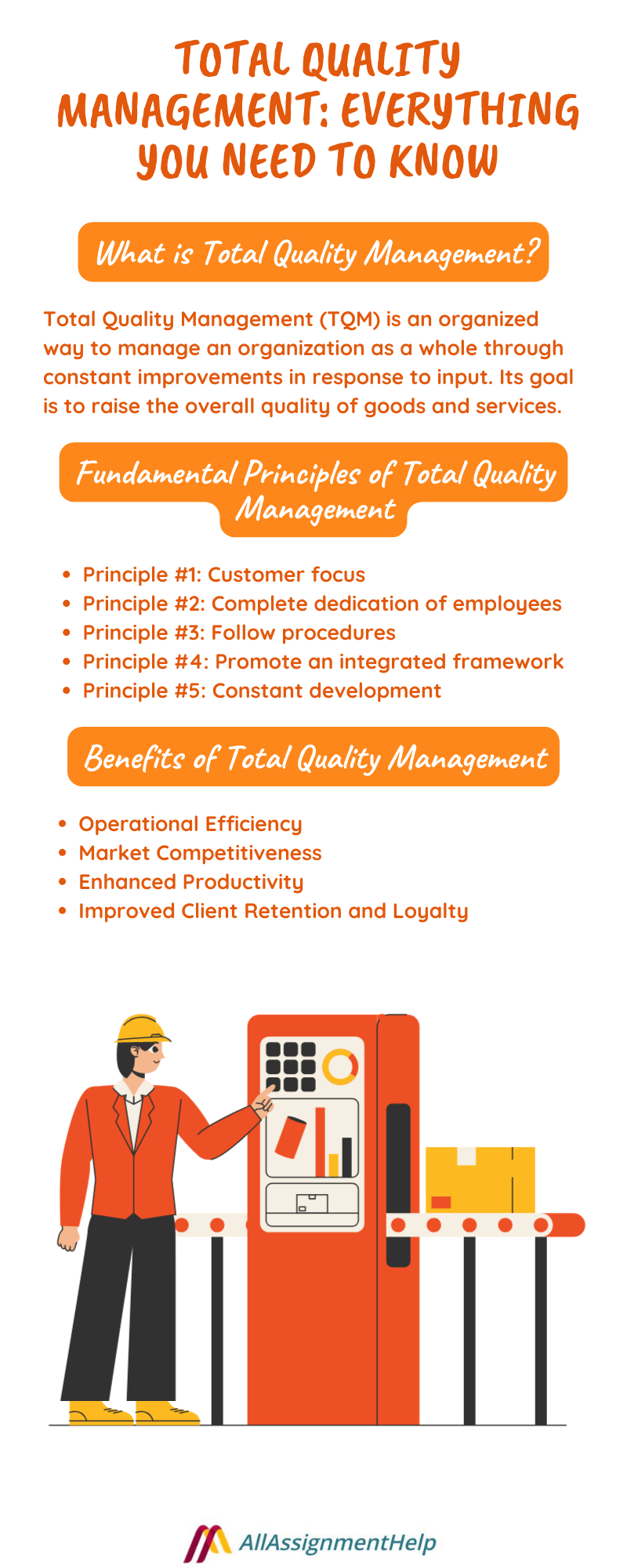
Fundamental Principles of Total Quality Management
The foundation for a successful implementation of TQM is a set of essential TQM principles. These are:
Principle #1: Customer focus
Knowing what your customers want and need will help you determine what goods, personnel, and procedures to use to meet and beyond their expectations. However, the use of this principle necessitates conducting study to comprehend the requirements and expectations of your clientele, coordinating organizational goals with those demands, measuring customer satisfaction, and soliciting feedback from them to inform future improvements.
Principle #2: Complete dedication of employees
Every employee should be pursuing shared goals. Workers are the heart and soul of any business. Hence, when they actively participate, their potential to enhance company culture, services, products, and procedures is maximized. This principle can be achieved by clearly outlining your objectives, encouraging each team and individual to take accountability for problems, and comparing your performance to your own goals and objectives.
Principle #3: Follow procedures
Ensuring that all members of the organization perform the appropriate actions at the right times is crucial for maintaining consistency and accelerating productivity. This principle will require you to assess and evaluate your present procedures to identify areas for improvement or areas where blockages need to be removed. Also, you must assess the potential effects of your procedures on every one of your stakeholders, including suppliers, employees, and customers.
Principle #4: Promote an integrated framework
Each business has a different work culture. However, it is nearly hard to achieve excellence in products and services without cultivating a high-quality culture. TQM focuses on integrating multiple procedures into an integrated framework. This approach incorporates components of company improvement to continuously improve and exceed expectations. You can this principle in more detail by taking a total quality management assignment essay writing service from an expert in the same field.
Principle #5: Constant development
TQM is centered on continuous improvement. Businesses need to always be looking for methods to make their operations, goods, and services better. This involves a dedication to lifelong learning and adaptation. However, this principle can be put into practice by putting rules in place that set quantifiable targets for system, process, and product improvements at the departmental, team, and individual levels. Moreover, it is essential to acknowledge and promote inventive resolutions to problems.
By following these aforementioned TQM principles, organizations can develop a culture of quality that encompasses all levels and functions and promotes long-term success.
Key Requirements for a Successful Total Quality Management Process Implementation
Implementing the TQM process requires:
- Planning Phase: Employees are required to raise any inquiries or problems during this time and get them resolved. The staff members inform the management about various difficulties they encounter in their daily work. Also, they explore the underlying source of the problem.
- Doing Phase: The workers in this phase come up with a fix for the problems that were found during the planning stage. Problems with employees are addressed through the development and application of strategies. Furthermore, at this phase, solutions and tactics are also assessed for efficacy and efficiency.
- Checking Phase: In this phase, a before-and-after comparative analysis is carried out to evaluate the efficacy and gauge the outcomes procedures.
- Acting Phase: This is the final phase of the process, where workers record their outcomes and get ready to tackle fresh problems.
Understanding these phases is necessary for writing informative TQM assignments. We suggest you to hire an expert if you are lacking behind any phase.
Essential Tools of Total Quality Management
With the use of the essential TQM tools, anyone can collect data to identify the majority of problems and provide potential solutions, even those without any statistical background. The essential TQM tools are as follows:
- Check Sheet: This form is pre-made and intended exclusively for data that recurs repeatedly. It is not suitable for collecting other types of data over time.
- Pareto Chart: This chart suggests that 20% of causes account for 80% of problems. It assists you in determining which problems fit into which groups.
- Control Chart: This chart illustrates how procedures and outcomes vary throughout time.
- Histogram Bar Chart: This shows the reason for problems’ frequency as well as the manner and locations of the result concentration.
- Scatter Diagram: This diagram presents data on the x and y axes to see how the factors affect the outcomes.
Businesses can achieve high quality in their goods and services as well as ongoing improvement by using an efficient total quality management tool.
Benefits of Total Quality Management
The following main advantages demonstrate why TQM is a smart move for every business aiming for excellence.
Operational Efficiency
Organizations can cut expenses, get rid of waste, and minimize inefficiencies by reviewing and enhancing their processes. This leads to improved resource usage and more productive production cycles. Moreover, it enhances overall operational excellence.
Market Competitiveness
Businesses that use Total Quality Management have a stronger competitive advantage. They can establish a solid reputation, draw in new clients, and keep hold of current ones by continuously providing top-notch goods and services.
Enhanced Productivity
TQM places a high value on approach performance and optimization. TQM helps businesses increase production by identifying and eliminating inefficiencies, optimizing workflows, and enhancing standard operating procedures.
Improved Client Retention and Loyalty
One essential component of TQM is customer attention. Businesses can build closer bonds with their clients by putting the needs of the consumer first and working to address those requirements on an ongoing basis.
Nowadays, total quality management is a widely recognized course among students. Also, many universities have started offering online TQM courses across various levels. Students are taking online courses to pursue a career in this area. However, taking online classes comes with multiple challenges. Students often search on the Internet, can someone take my online course for me? We want to tell such students that there are multiple services available who are always there to help you with your online TQM course and classes.
Examples of Total Quality Management
There are multiple examples of Total Quality Management (TQM) that can be found in modern quality management methodologies. A few of those examples are as follows:
Toyota Production System (TPS)
Toyota set Total Quality Management (TQM) in 1961, and it is often cited as a model of TQM. TQM placed an intense focus on respect for people, waste reduction, and continual improvement. Furthermore, it incorporates techniques like Kaizen (continuous improvement) and Just-in-Time manufacturing to increase the effectiveness and quality of production processes.
Motorola’s Six Sigma
Back in 1986, Motorola created the Six Sigma process. It is a quality control method that aims to lower process variance and defects. Several sectors have widely embraced this management system and process thinking methodology to promote quality improvement.
Healthcare Sector
The implementation of TQM concepts by hospitals and other healthcare facilities aims to improve patient care, lower medical errors, and simplify operations. Patient wait times can be decreased or emergency room operations can be more efficiently run by applying Lean Six Sigma approaches.
You can read about these examples in more detail on the Internet. However, there are more such examples of Total quality management for you to know to hold a better grasp of the topic. These examples will help you understand the strategies and measures a business takes to enhance its product and customer satisfaction.
Also Read: Project Management Assignments: Phases and Templates
Final Thoughts!
Total quality management focuses on exceeding expectations in quality in addition to achieving organizational goals and enhancing performance. Any business regardless of size or sector can successfully implement TQM with the correct tools and practices.
However, TQM is not an easy field to conquer alone. Therefore, students are suggested use academic writing services to get quality assignments completed before the deadline. We also help students with online classes and exams. Anyone enrolled in online TQM classes can get help from our experienced online class takers. Apart from TQM, they can also ask us to do my online calculus class, economics class, biology class, or any other they need help with.
FAQs
Why total quality management is important? TQM is important as organizations could develop and maintain long-term success for customers and themselves by requiring all employees to concentrate on quality management and continual improvement. |
What is the fundamental idea behind TQM? Continual improvement of all aspects and functions within a company is the goal of the strategic idea of total quality management. |
What are the goals of Total Quality Management? The goal of Total Quality Management (TQM) is to achieve excellence across the board for an organization by methodically getting rid of waste, cutting down on errors, and enhancing customer happiness. |